Controlling Quality
About Our Brand Inspection System
The Nichirei Group conducts quality inspections in an effort to ensure food safety, food defense, and the prevention of food-related fraud to maintain customer trust in the safety and quality of our products.
The Nichirei Foods and Nichirei Fresh Quality Assurance Divisions check product quality by carrying out factory and product inspections.
Factory inspections confirm whether the rules and systems as applied to factory development, production facilities, production, and logistics are being followed and correctly implemented.
Meanwhile, product inspections are used to confirm whether food labeling, ingredients, and product standards (regarding such items as microorganisms, residual pesticides, allergens, and packaging materials) comply with the relevant regulations.
This system of quality checking ensures that only products that have passed inspection are approved for sale.
In addition, the Nichirei Corporation monitors the inspection results to confirm whether Nichirei Foods and Nichirei Fresh are appropriately managing their quality assurance systems.
Nichirei Group Quality Control System
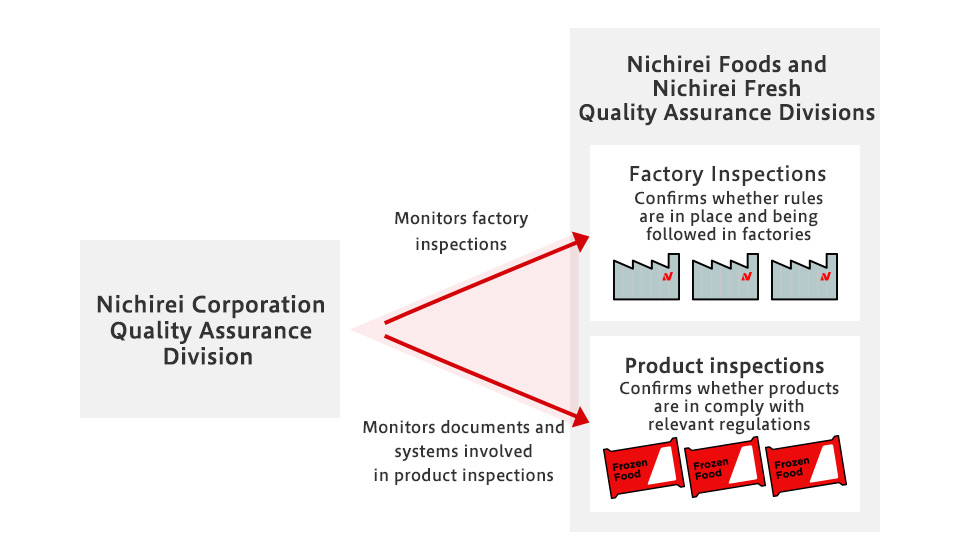
Factory Inspections
These inspections confirm whether the rules and systems as applied to factory development, production facilities, production, and logistics are being followed and correctly implemented as indicated below.
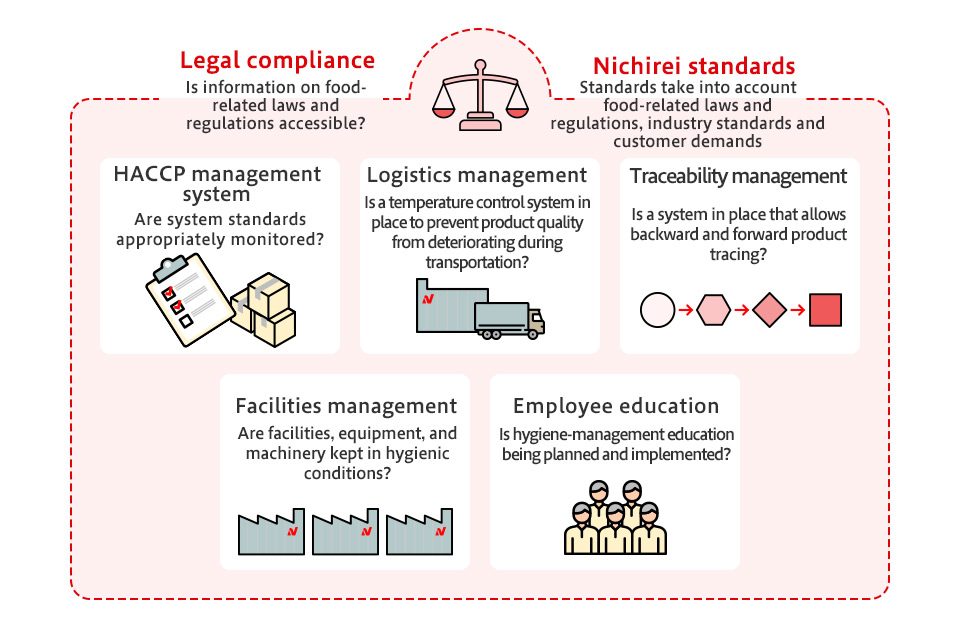
Product Inspection
Product inspections are used to confirm whether food labeling, ingredients, and product standards (regarding items such as microorganisms, residual pesticides, allergens, and packaging materials) comply with the relevant regulations.
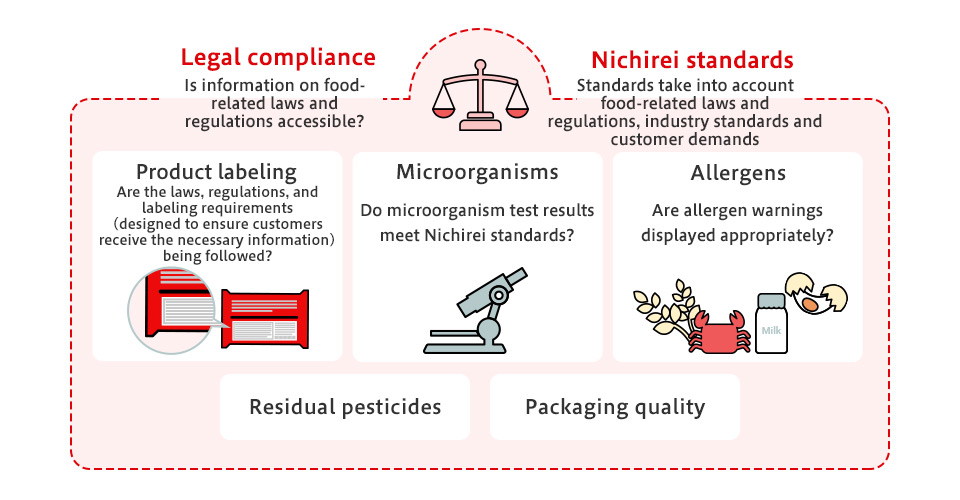